In den letzten Beiträgen haben wir den Einsatz des 3D-Druckers im Fertigungsbereich beleuchtet. Aber natürlich soll er auch in der Entwicklung unterstützen.
Im ersten Moment denkt man dann schnell an Gehäuse oder andere Platinenaufnahmen, in welche elektronische Baugruppen geschoben werden.
Das genaue Gegenteil von dem haben wir mit unserem 3D-Drucker praktiziert.
Ausgangssituation
Im Zuge der Abkündigung eines Gehäuses waren wir gewillt, unserer kompakten 1TE-breiten Pegelwandler umzudesignen. Der Grund war nicht nur allein das Gehäuse, auch konnten wir so bekannte Optimierungspotentiale erschließen und für noch mehr Robustheit sorgen. Außerdem steht uns so zukünftig die Option Federkraftanschlusstechnik zur Verfügung.
Klassisches Re-Design
Ein Re-Design kann von diversen Dingen ausgelöst werden. Bauteilverfügbarkeiten, Abkündigungen, Fehlern im Design oder auch einfach wegen Optimierungsmöglichkeiten. In der Regel wird hier versucht, den Großteil zu übernehmen und nur an den relevanten Stellen zu ändern.
Auch wir gingen hierbei so vor.
Das alte Design wurde weitestgehend übernommen. Natürlich mussten wir wegen des neuen Gehäuses maßgeblich die Mechanik, also die Form der Baugruppe und die Lage der Bauteile anpassen. Die elektronische Schaltung selbst blieb fast unverändert.
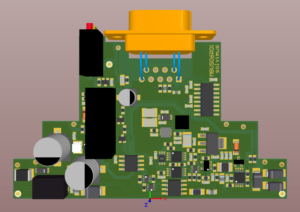
vorher
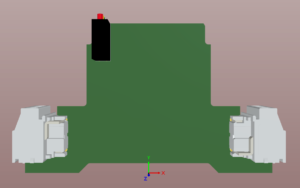
neuer Formfaktor
Nachdem wir nun die neue Leiterplattenkontur übernommen hatten, mussten wir die Bauteile lediglich neu anordnen. Etwas Geschick war gefragt, denn das neue Gehäuse bietet etwas weniger Platz als vorher. Aber wir sind es gewöhnt, Baugruppen sehr eng zu packen. So entstand in kurzer Zeit das neue Design.
Da die Schaltung übernommen wurde, konnten wir auf einen elektronischen Prototyp verzichten, das Risiko war sehr gering, dass sich bei Layouten Fehler eingeschlichen haben. Aber passt die Baugruppe auch wirklich in das neue Gehäuse?
Genau hier war das größte Risiko zu sehen. Daher entscheiden wir uns, na klar, für einen 3D-Druck der Baugruppe.
Druck einer Baugruppe
Dank unseres Entwicklungstools stehen von allen Baugruppen 3D-Modelle zur Verfügung. Also ab damit in den 3D-Druck.
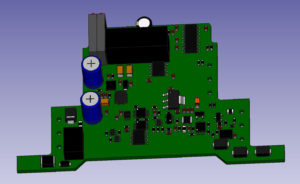
3D-Modell im CAD-Programm
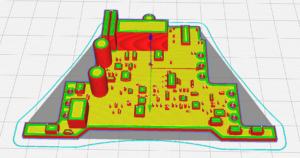
3D-Modell als Druck-Programm im Cura
Der 3D-Drucker war nun ca. drei Stunden beschäftigt. Deutlich schneller als Leiterplatte bestellen, Bauteile einkaufen und dann Prototypen bestücken.
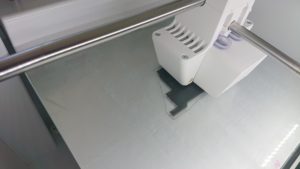
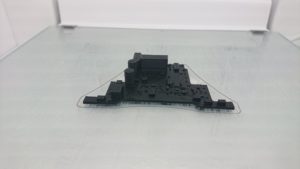
Baugruppe im 3D-Druck
Das Resultat war vielversprechend. Der Druck bildete die Baugruppe und die Bauteile sehr gut ab. Ein Vergleich mit einer realen Vorgängerbaugruppe bestätigte den Eindruck: als mechanisches Muster ist der Druck sehr gut geeignet.
Prüfung der Mechanik
Zunächst prüften wir, ob die neu eingesetzten Steckverbinder/Anschlussklemmen passen. Die bemusterten Steckverbinder steckten wir dann einfach in die Löcher in der gedruckten Baugruppe. Und siehe da: passt. Auch für die Bauteile blieb genug Platz.
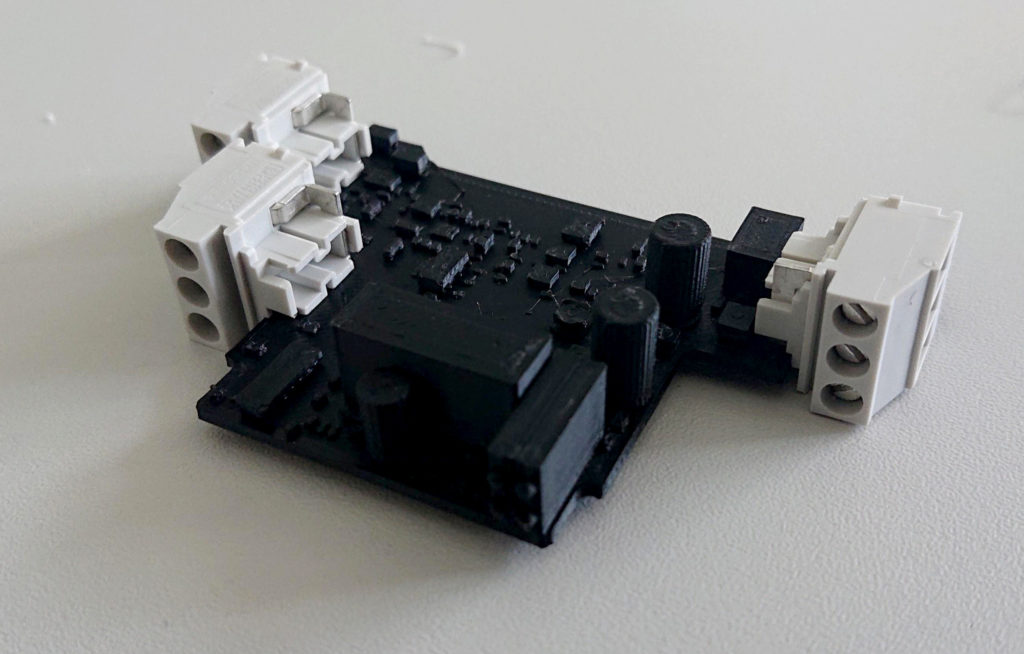
gedruckte Baugruppe mit aufgesetzten Steckverbindern
Nun der zweite Schritt. Passt die Baugruppe auch in das Gehäuse? Laut Entwicklungstool ja, aber real, mit allen Ecken und Nasen an Leiterplatte und Gehäuse? Die gedruckte Baugruppe wurde mit gesteckten Steckverbindern dann in das Mustergehäuse eingeführt. Knapp, aber es passte.
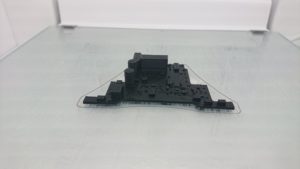
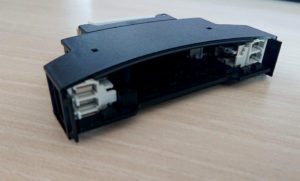
gedruckte Baugruppe im Gehäuse
Zumindest im ersten Moment. Das Gehäuse verfügt über eine aufklappbare Gehäusefront. Diese Klappfunktion nutzen wir zwar nicht, aber dies vereinfacht die Montage. Durch die Form der Leiterplatte war das Klappen allerdings nicht möglich. Eine Ecke der Leiterplatte ragte über den Drehradius der Gehäusefront. Das haben wir vorher im Entwicklungstool nicht festgestellt, da dort die Front immer geschlossen war. Genau deswegen war es gut, den Druck durchgeführt zu haben.
Die störende Ecke der Leiterplatte wurde dann nochmal im Design verändert. Der Platz war gegeben.
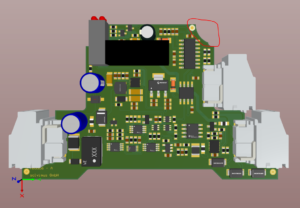
finales Design der Baugruppe
Resümee
Durch die Prüfung mit realem 3D-Druck erkannten wir einen mechansichen Designfehler bereits vor echter Produktion einer elektronischen Baugruppe. Auch wenn der Fehler im Produkt nicht gestört hätte, wäre die Montage erschwert gewesen.
Durch den Einsatz des 3D-Drucks wurde uns dies erspart und es wurde kein zusätzlicher Designzyklus nach der Erstbestückung notwendig. So konnten wir typische Entwicklungszeiten signifikatn verkürzen.