Im letzten Teil zeigten wir, wie wir eine Kabel-Wickelhilfe zur Unterstützung in der Fertigung geplant und konstruiert haben.
Die Spannung steigt, nun wird gedruckt. Wie sehen die Objekte gedruckt aus? Ob die Konstruktion korrekt war und die Teile zueinander passen? Funktioniert das Wickeln?
Dann schauen wir mal.
Der erste Druckversuch
Wir laden also das 3D-Modell in die Cura-Software. Mit 209 mm x 180 mm Grundfläche ist das Modell doch recht groß. Aber es ist ja so dimensioniert, dass es in den Druckbereich passt. Der Halter und der Drehteller werden positioniert und der Slicer in Cura gestartet.
Daraus ergibt sich dann folgendes Druckprogramm:
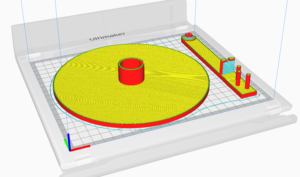
Die Berechnung sagt, dass der Drucker knapp 22 Stunden dafür braucht. Da kann man nur hoffen, dass über Nacht nichts schief geht.
Also starten wir mal.
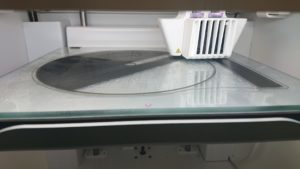
Schicht für Schicht wächst nun der Druck. Es sieht gut aus. Um am nächsten Tag ist es fertig:
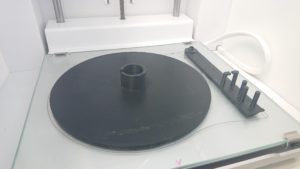
Sieht so aus wie es erwartet war. Die Unterseite hatte an manchen Stellen die Haftung zum Druckbett verloren, aber das sollte nicht stören.
Ob das funktioniert?
Als erstes probieren wir den Rastmechanismus. Hier haben wir ja einfach nach Gefühl konstruiert. Klack! Der Drehteller rastet ein, hält auch ganz gut auf dem Halter und er lässt sich drehen.
Cool, funktioniert wie gedacht. Mit stolzer Brust geht es nun also in die Fertigung.
Unser erster Wickelversuch
Nun wird sich zeigen, ob die Konstruktion für den Praxiseinsatz tauglich ist. Der Halter mit Kabelbremse und Kabelniederhalter und auch der Drehteller müssen sich nun beweisen.
Wir wählen einen Schraubstock, um den Halter zu arretieren und legen dann das Kabel ein. Das passt perfekt in die Kabelaufnahme:
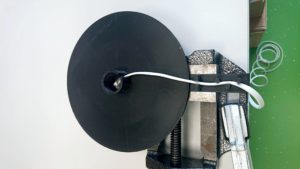
Dann wickeln wir mal…
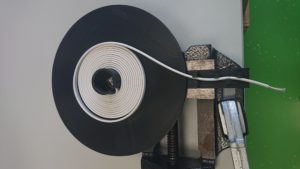
Und tatsächlich es funktioniert. Das Kabel wird durch die Bremse auf Zug gehalten und wickelt sich somit gleichmäßig auf dem Drehteller auf.
Nur das Entfernen der Kabelrolle zeigt sich als schwierig. Es ist doch relativ straff um den inneren Zylinder gewickelt. Dadurch ist die Reibung hier sehr groß und das Kabel lässt sich nicht gut abziehen. Bei den ersten Versuchen gehen einige der Kabelrollen wieder auf.
Hier kommt nun die Kurbel ins Spiel.
Die Kurbel
In der Konzeption war die Kurbel bereits vorgesehen. Doch jetzt muss sie so konstruiert werden, dass das Lösen der Kabelrolle vom Drehteller einfacher geht.
Unser Ansatz: die Kurbel vergrößert punktuell und nicht flächig den Wickelzylinder. Also wird diese über den Wickelzylinder des Drehtellers gestülpt.
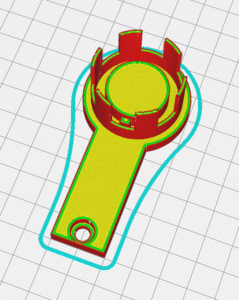
Zur Führung dienen ein innerer Zylinder und eine Rastnase, passend zum Drehteller. Der äußere Zylinder bildet die unterbrochenen Auflageflächen für das Kabel. Dadurch sollte die Reibung des Kabels ausreichend verringert sein.
Ein Loch in der Kurbel dient der Befestigung eines Drehknaufs per Schraube.
Gedruckt ist die Kurbel relativ schnell. Danach ist das Ergebnis höchst zufriedenstellend:

Produktiveinsatz
Erste Wickelversuche waren sehr positiv. Doch wie ist es im Produktiveinsatz? Mehr als 1000 Kabel waren aufzuwickeln. Ist unsere Konstruktion serientauglich?
So viel in Kürze: Ja, sie ist es.
Der Aufbau funktioniert sehr gut. Nach etwa 200 Wickelungen zeigten sich dann Abnutzungserscheinungen. Der Rastmechanismus des Halters schwächelte als erstes. Diese ersetzten wir kurzerhand durch eine Maschinenschraube.
Dann brachen auch noch zwei der umlaufenden Stege der Kurbel. Das gewählte Material Tough PLA war wohl zu spröde. Ein zweiter Druck mit Nylon als Material zeigte mehr Robustheit der Kurbel.
Resümee
Alles in allem war die Kabelwickelhilfe ein sehr interessantes Projekt. Die Konstruktion eines solchen Hilfsmittels war für uns neu. Das Ergebnis jedoch konnte sich sehen lassen und hat die Arbeit in der Produktion deutlich vereinfacht. Genau das was es sollte.
Dies macht Lust auf mehr. Sicher werden wir uns selbst das eine oder andere Hilfsmittel zukünftig selbst drucken. Etwas Erfahrung zu Konstruktion und Materialwahl benötigen wir aber noch.
Die Serie wird uns weiter begleiten. Im nächsten Teil zeigen wir den Einsatz des 3D-Drucks im Umfeld der Produktentwicklung und wie man dort Desingzyklen sparen kann.